以下是现场速记。
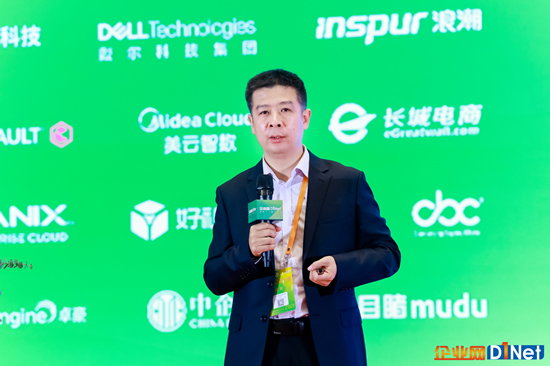
亚明汽车CIO 肖庆阳
肖庆阳:各位CIO的同仁们,大家下午好!听了将近两天的时间,感觉收获不少,终于该轮到我了。
我接下来的分享可能是和之前的这些大佬们稍有一些不同的地方。因为我是来自于企业,在企业做了多年的CIO,所以说我们这个数字化转型之路可能是更加的结合我们的实际公司生产经营。所以说希望通过我接下来的分享能够给工业制造企业带来一些启发。有些观点可能我们也可以相互的交流,进一步的交流、探讨。
首先自我介绍一下我来自大连亚明汽车部件股份有限公司,在我们公司我也是一名老员工了。从事二十多年CIO的工作,一步步把企业从信息化为零开始一步步建设成国家级工业互联网试点示范企业,在我们数字化转型之路上我们也有很多的体会。接下来我会给大家进一步的交流!
首先给大家介绍企业背景。我们是一家传统的汽车零部件生产的企业,产品下面会有介绍。亚明汽车近几年来我们通过数字化转型之路,我们承担了一些国家级的科研项目,包括国家智能制造新模式项目,这是2017年。2018年国家重点研发计划项目以及工业互联网创新发展工程项目,在这些项目建设过程之中,我们为了完成国家任务在信息化上大力的进行投入,做了很多的工作。
通过20多年的数字化的建设,目前亚明汽车虽然说我们是一家小企业,但是在我们国内的同行业当中我们还是处于领先的水平,数字化程度还是比较高。
首先介绍一下公司,大连亚明汽车部件股份有限公司是一家以压铸件生产以及压铸模具设计与制造。我们公司有近70年的历史。我们主要生产的产品是以汽车动力总成压铸件为主,像变速器、油底壳、钢铁、缸盖这些零件,主要客户是奔驰、大众、福特等整车厂。近些年我们开始研发新能源三电产品。
这是我们客户情况以及公司生产的产品,大家看我们的客户都是一些顶级的国际上的汽车厂,包括我们现在最大的是丰田,第二是奔驰、大众、福特,近些年我们又开发了像特斯拉以及沃尔沃新能源的汽车主机厂。
右边是我们生产的零部件,大家看到是以铝合金压铸件为主,它是铝合金首先通过压铸工艺然后进行精加工。目前我们在新能源市场上呈增长的趋势。
这个是我们即将建设新的工厂,大家看到我们有近70年的老厂房,这个厂房目前面积也非常小,已经无法适应我们下一步的企业发展。所以说我们在经济开发区正在建设7万多平的新工厂,新工厂主要以新能源汽车三电产品为主的生产。
对于企业来说,我们经过近些年的承接的国家项目以及数字化的转型,目前已经初步形成了数字化、网络化和智能化的生产模式。同时,亚明汽车也是中国国家亚洲前20强企业,也是国家零部件出口基地。目前我们也拿到了国家5G+工业互联网第一批典型解决方案的提供商。
为什么我们会成为提供商?后面我会介绍,因为通过我们数字化转型之路,我们现在也对外赋能,给其他的企业赋能来进行数字化的解决方案的提供。
数字化转型的背景,通过这两天跟许多大佬们一起分享、交流,大家其实对数字化转型的趋势以及企业的动力都已经谈得非常透彻了。
我们的背景可能是有企业自身的发展原因,这里我也给大家分享一下。
首先我们是一家传统的汽车零部件的供应商,作为一家汽车零部件的配套厂来讲,我们的顾客就是主机厂。主机厂对我们有很苛刻的要求,大家看我列举的主要的有三个:
第一个是准时交付。因为我们的客户,你想他的奔驰、丰田生产线,每天根据生产计划进行拉动生产,所以他绝对不允许出现停线的情况。我们作为配套的汽车零部件厂要求必须准时供货,我们的生产计划是一个滚动的计划,大概每个月、每周甚至细化到每一天都有一个精确的交付的数量。这个对于我们来说是必须要给客户保证的。
大家可能不知道如果由于我们的供货出现对于客户主机厂的停线,他会产生一个高额的索赔,大概一分钟是2000块钱,所以说风险非常大。
第二个他对品质的要求非常高,要求的是零缺陷。就是我们供给主机厂汽车零部件不允许有一件出问题,因为汽车关系到人民群众生命财产的安全,我们谁也不希望我们在4S店买到的汽车在行驶的路上出现发动机的故障,所以这个对于质量的要求非常高。
另外对于年降。大家可能不太清楚这个词,汽车主机厂要求我们所有零配件供应商每年要降价,而降价的幅度是由主机厂来提出的,就是这么霸道,没有办法。因为顾客就是我们的上帝。
所以说针对于这些来自于主机厂对汽车零部件、工厂的这样的一些要求,作为零部件企业如何来应对?这也是我们最初搞数字化转型我们的一个初衷和目标。
作为传统的制造工厂来讲,我想在座很多CIO都很清楚,我们制造工厂里面是一个什么样的情况。大多数企业,在早些年都是缺少数据支撑,决策靠猜测这么样一种情况,都是一种粗放式的靠人的经验来主观管理的情况,我们工厂在早些年也是这种情况。
那么怎么样满足客户对于我们的要求?所以说你在这种情况下你就没有办法来满足客户的准时交付、零缺陷以及年降的要求。
这也是我们最早搞信息化也好、数字化也好的一个初衷。
这张PPT我想在座更多的是CIO,我是做过一段时间生产的部长以及生产的厂长。我非常清楚,在我们的工厂里,各个的部门、各个角色他们有哪些具体的痛点。
比如说像工艺、设备、生产的以及我们的一些高管,他都有他的管理上的问题和痛点。针对于这些问题,我们能不能用数字化、信息化的手段来解决这些问题?我想这也许是更加实实在在企业数字化转型的一个总因。
随着近年来我们国家也提出来数字化转型将引领企业的未来,作为传统的制造企业工厂,实际大多企业CIO已经越来越意识到数字化转型是势不可挡的,终于来了。实际上企业的领导者现在也认为,企业数字化转型不是一道选择题,而是一道生存题。
我们去年在宁波一些企业进行同行企业推广我们解决方案时,有许多企业老板已经认识到这个层面了。企业不搞数字化确实是在等死,生存都存在问题,因为我们市场的变化,我们的客户、我们的行业在日新月异的产生深刻的变革。
所以说这个也是我们大连亚明汽车在数字化转型的一个初衷、动力。
接下来我跟大家再具体分享一下具体我们在转型过程中我们的做法,我们是怎么来做的,我们为什么要做?可能我讲述这些比较接地气,比较实用。
大连亚明汽车数字化转型发展历程也跟大家介绍一下,实际我们搞数字化是非常早的。我们在1996年时,我们企业就成立了信息中心,当时信息中心的职能它还有一部分的三维设计,因为我们在96年的时候就已经搞了三维计算机辅助设计。还有一块是信息化管理这一块,我们ERP在2005年时就已经上了,是非常早的,到现在已经有15、16年的时间了。企业接触信息化转型还是比较早的。
在2007年时我们压铸车间,下面的图是压铸生产已经实现了全自动化,不需要人,全部由机器人完成一个生产的过程。
在2010年我们的MES系统就已经上线,2017年我们又承接了国家智能制造的专项。
从以上发展历程来看,作为汽车零部件配套企业,因为它有的时候也是被我们的客户、我们的主机厂牵着走。2005年上ERP,因为我们作为福特的供应商必须具备数字化能力,销售订单必须和福特公司在网上进行EDI,它把订单传到ERP系统,我们发货时通过发货系统传到福特工厂。所以汽车零部件企业数字化开展比较早。
这个是我们亚明汽车总体的智能制造方案的架构,大家看到我们也是从智能化的设计、装备、制造以及经营这几个方面来实现管理的优化、升级。
最终目标是让制造企业搞数字化,还是实实在在的。我们的目标就是围绕着增效、提质、降本这三个层面实实在在的来做的。最终通过增效、提质、降本来完成客户对我们的要求,有对我们生产效率的提高、准时供货以及对成本都有要求。
数字化转型主要内容大概分九个方面:
第一个方面.引进了一些数字化和柔性化的自动化的生产线。
第二个方面.对一些老旧的生产设备进行智能化改造和数字化集成。
第三个方面.数字化关键技术制造的自主研发。
第四个方面.物联网的建设与数据采集。
第五个方面.车间制造执行系统MES系统的建设。
第六个方面.基于5G视觉缺陷建设。
第七个方面.数字化生产管控平台建设。
第八个方面.数字卵生与大数据应用。
第九个方面.AI工业检测工具应用。
第一个方面是必须要满足的,数字工厂已经不是靠几台车床就能完成的,我们现在全部是采用智能的压铸机以及智能机器人组成的,这个是重资产,投入非常大。
这里是我们压铸车间数字化装备的建设,目前我们压铸的车间,有的同事可能不太清楚。我们生产是铝合金压铸件,它需要吨位非常大的压铸机,整个压铸单元实现了压铸、切边、码垛、在线检测全自动化的无人生产,这个是我们智能工厂的第一步,首先要花钱买设备,然后把它做集成。
有一个简短的视频,也是我们整个压铸单元生产的全过程,它通过自动的切边、码垛以及我们的AGV运输,完成了无人化的全自动的生产。我们在数字化集成这个方面,我们通过自主研发的SCADA系统实现智能化监测和控制,通过在设备上加装了很多传感器,用于监测产品的品质。
像我们影响产品的关键指标:压力和温度,这些我们通过我们自主研发的采集系统,我们对于整个加工生产单元做了一个闭环的在线监测,实现实时控制。
右边的是我们机台的主要生产参数的看板。
这个是我们自主研发的压铸冷却水可视化控制系统,获得了大连市专利奖一等奖。我们加装了大量传感器包括温度、流量传感器,来对这些影响生产的主要的工艺参数进行监控。我们的数字化实际包括了管理的数字化和工艺的数字化,这个属于工艺的数字化,它也是靠传统。
以前当模具冷却水出现故障时,往往是靠人去定期的巡检,才能够发现比如说温度不够或者压力不够。这个时候很容易形成批量的质量问题,让企业受到很大的损失。这个项目也是我们IT部门和工艺部门联合完成的。
大家看右边通过IT的技术和OT的结合,我们就能够不用人去点检,随时实时的对整个的模具生产状态进行一个可视化的监测和控制。这样最大程度上提高产品的品质、降低我们不良品的发生。
这个是我们机加工车间,目前有230台套柔性加工设备以及我们的智能物流,我们现在全部把它设备、机台全部联网,实现了数据的实时采集。
这个是工业互联网互联互通的建设,目前工厂的设备层和我们的办公网络它实际上车间是两套网络,全部已经实现了数据的采集,包括工厂内部的人员、物料以及工艺、环境等等数据的采集我们都已经做了。
这个就是我们做的设备生产数据的采集与监控系统,大家看到上面是我们的设备商的PLC以及采集的模块,以及我们后来自己加装的传感器。
大家有些工业企业的朋友可以看到我们生产的设备比较老旧,可能十几、二十年的设备都有,怎么实现数字化的物联?我们有时可以通过加装传感器,目前的传感器品类比较多,温度的、压力的、流量的以及IO的采集的,实际上非常多,成本也不高。我们通过传感器的加装,就可以在下面实现设备的互联互通。这些数据全部实时上传到数据中心。海量的数据也可以进行工艺分析和优化,提高产品的品质。
另外最关键一点,有些设备如果出了问题,我们可以通过IT系统主动的推送报警来及时的发现,变被动的反应为主动的预防,这个是很重要的。
这里就比较容易了,我们通过对生产过程的数据采集,我们把人机料法环测这些数据通通打通,把它采集上来。大家可以看我们的人员,一卡通。从员工的考勤、就餐以及到车间的包工全部采用一张卡就把人的信息连到了网络里面来。物料我们在有一些零部件上打印了激光的二维码,像这个图片是我们零件的二维码。还有我们通过在周转箱上张帖二维码的方式完成扫码入库领料的操作。
我们原来ERP系统往往靠人工录入单据,这样数据滞后,而且数据不是很准确。通过扫码的方式和ERP、MES系统打通,就实现了数据的及时采集,实现了物流和信息流的同步。
关于MES系统,我这两天在吃饭的时候也听见好多的CIO朋友在聊这个MES系统。这个MES系统确确实实因为它不是一个标准化的系统,可能每一家企业、每一个行业都不一样,所以说实施MES的风险还是比较大的。
我们亚明汽车采用的是自主开发的方式,我们有自己的研发团队,这些年我们在MES上主要还是自下而上的这么样一种开发模式。我们从了解实际的业务需求,了解设备情况,了解工艺情况,所以说我们自己通过自主研发的方式构建了我们生产过程的一个MES系统,解决了我们的生产效率、产品质量和生产异常这样的一些功能模块。
用了效果还是比较好的,因为我们是自己给自己开发,给自己应用,我们会不断的完善。目前很多同行到我们工厂来参观的时候也比较看好我们这套系统,目前我们MES系统也已经推广到我们的同行业的企业当中去。
这里是一个可视化的生产指挥中心,通过采集上来的这些设备数据、人员的数据以及物料以及工艺的数据,我们就可以来做可视化的生产管控中心。
大家看到我们做了非常多看板,这些看板全部在车间的现场。而且我们这个看板,大家可以看到,我们这个看板不是一个冷冰冰的大屏,我们是有人的。人可以在上面操作,看板实际上也是一个终端。
为什么要做这么多的看板?有一次我到我们的客户-一汽丰田那里去参观考察。当时令我非常震撼,因为一汽丰田车间厂房首先是5S做的特别好,它整个机加和压铸车间地面,当时我用手摸了一下,一点灰都没有。日本企业做得非常好,但是百分之我非常诧异的是,不是很大的机加工车间有非常多的看板,当然它这个看板是传统的纸制的,它用了很多卡片,每一天很多的工人去看板上做记录。
所以当时座谈会交流的时候我就问日本人,为什么丰田车间会有这么多的看板?工人干活同时还要经常到看板上去写写画画,我说这个是怎么考虑的?当时日本人给我的说法对我来说受益很大。他说看板不是给领导参观看的,这个看板是我们发现问题和解决问题的一个平台。们通过看板上的文字、表格、颜色我们就知道生产现场发生了什么,有哪些问题,应该谁来去解决?所以它实际是一个平台和工具。
回来之后我们也做了大量的看板,大家可以看到我们看板上也有很多颜色、文字、进度条,而且这些看板在现场能够一目了然,我们的车间管理者、领导还有工人、员工随时随地会看到我们生产过程当中异常的情况、设备的情况、工艺的情况。效果还是非常好的。
这里我们也是跟丰田学习了安灯的系统,一汽丰田主要采用的是安灯系统。我们自己开发做了改良,系统也是和我们机台全部联网,当机台发生异常时候,我们传感器探测出设备,比如说有机械故障或者是电器故障的时候,首先它会自动的采集到这个状态。
如果是说这里有复杂的问题,我们通过员工在现场的呼叫,它就会自动的给我们运维人员发送手机的短信或者直接会拨打一个电话。这样,我们的运维人员会及时的处置提高生产效率。
像我们重资产企业我们生产设备要求24小时不停机,因为我们要保证产量,保证交付能力,设备运维是非常重要的。以往设备出问题时往往处置时间会非常长,尤其信息也不透明,这样对现场的执行力是很不够的。上了这个安灯系统之后,我们大大的有效的提高了现场的执行力。
这套系统用的也是非常的好。我们在物料这一块,在物料流转这一块,大家知道ERP系统它有物料入出库功能。昨天我还和一位CIO朋友在聊,我说你们这个ERP系统帐物相符吗?入库单准吗?他说有部分时间段是准的。作为汽车零部件来讲我们每天是拉动式生产,必须确保账物相符,我们采用打码、扫码方式直接和ERP系统同步,保证物料、领料、入库和系统和实物是同步的。
简单介绍一下这个,通过引进两台AGV车,完成压铸车间到物料的实时配送。
这个是我们的生产指挥中心,我们的系统现在实现了管理驾驶舱的功能。这个是在手机端、移动端,我们也实现了信息的主动的推送。
这个是一个车间的数字卵生系统,在我们产品生产车间,左边是虚拟产线,右边是物理产线,这个车间是黑灯车间,平时没有人。所以我们运维人员可以在监控室里面看到车间生产运营情况。
这个是我们基于5GAI视觉检测系统,我们通过在现场安装工业相机对零部件进行拍摄,拍摄完之后会把数据通过5G,通过在云端进行比对。
对于数字化转型的效益来讲,从提质增效降本,对于企业竞争力的提升作用还是非常明显的。
我们现在数字化解决方案,我们也专门成立了一个研发的团队,我们现在数字化解决方案给同行业进行赋能。我们最近在2021年时也对外签订了1千多万元的订单,用我们这个数字化研究成果目前对外进入复制和推广阶段。
对于数字化转型有五点体会:
首先是企业领导者依然要有战略的决心来做这个事儿。
第二以人为中心。我们说企业里面实际上看似一套冰冷的系统,实际上它是和人是密不可分的,我们只有提高我们的员工的整体意识,对数字化转型的认识,它才能够起到比较好的效果。
再有业务流程的再造,实现一个数据去驱动决策,这个我想CIO们大家都有一定共识。
最后一个敢于试错,持续改进。
数字化转型大家都已经达成共识,它是势不可挡的趋势。数字化转型对企业来讲,像我们企业经过实践来讲我们觉得它不是一蹴而就的。对于我们来讲我们要有这方面的认识,我们仍然还需要不断的探索,不断的创新,来把我们数字化转型越做越好
我的分享就到这儿,谢谢大家!