以下是现场速记。
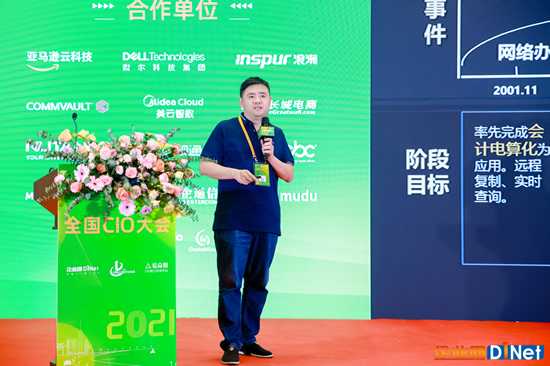
天瑞集团信息科技有限公司副总经理 马俊峰
马俊峰:前面几位大咖分享的时间有点长,给我留的时间、空间比较小,我想问一下在座的各位CIO,属于流程制造的能不能举一下手?还挺多的。自认为属于传统制造企业的,有哪些?我们就进入我们企业在数字化转型的经验,我给各位大咖做一个分享。
我们今天主题主要是流程和传统。主要通过三部分:天瑞集团简介以及信息化建设历程、工业互联网创新。
天瑞集团始创于1982年,经过三十余年的发展,已成为集旅游、水泥、铸造、互联网物流为主体的股份制企业集团。我们今天分享主题重点是针对水泥行业。
今天大咖讲了企业未来发展最重要的是科技型企业,我们从完全的传统制造型企业开始向科技型企业迈进。
第一.我们集团在01年是网络办;07年定的目标是财务业务一体化,那时先把ERP上起来,我们那个时候用的是用友NC5系列,基本从5系列第一个版本用到最后一个版本;13年我们启动了叫数字水泥与集团管控项目。这个目标非常明确:第1.我们要把原来所有没有数字化的数据要收集上来;第2.集团管控。集团要对下面的企业很多的权利要上收到集团来进行统筹管理;
15年连续启动工程项目、物资直采、仓储平台、电子商务等建设,是13年项目后续延伸;16年启动智能工厂和网络货运。大家可以看15年、16年是有大事件发生的,我们集团13年才正式成立信息化部,15年成立了信科公司就是天瑞集团信息科技有限公司,作为一个科技的公司去独立的运营。16年我们又成立了两家公司,我们在信息化部下已经有三个科技公司了。
17年我们启动了财务共享、税务信息化(增值税发票部分的业务);18年做了工业互联网平台,开始工业互联网平台的建设。通过这个过程,主要给各位CIO分享,一个集团企业根据业务战略的发展启动了不同的项目,包括人员的配备、公司的投入,整体来说是配套的动作。
同时企业从01年刚开始做信息化到18年到去年、今年做这么多之后肯定会有很多的问题,所以才会有这样的四梁八柱的规划架构。
首先.业务架构、应用架构、技术架构、数据架构,这是对整个集团所有的业务需要管控,它体现的最重要的理念是,开始很多CIO说没有系统,这个系统没上,那个系统没上。但天瑞已经做到基本所有业务系统都有了,但这个时候面临很大的问题。第一.系统迭代更新的问题;第二.IT治理,所有的业务管理会出现有很多的问题,衔接的问题、牵一发动全身。这个系统改一下可能对整个后端业务改动非常大。
同时反馈所有CIO面临的问题,大家都在建平台,建系统,最终我们建的是非常沉重的平台或者系统。这个平台沉重到一定程度,它是不能迅速适应一个企业的变革。数字化转型这个概念,我更喜欢叫它为数字化变革,变革就是变化、革命。企业最重要是要变化还有革命。
每一次IT在做事情,都是在革自己的命、革业务的命。所以所有的说IT项目都是一把手工程,都是CEO的工程。因为CEO对企业的未来,它是第一责任人,它需要对这个企业的未来做负责。
所有的项目都是为了企业的战略的使命,基于这个战略要实现什么打造什么样的能力,我们才去上什么系统。所以说我们CIO的衣食父母其实就是用户。用户提的需求,才是我们的核心。
简单讲述一下我们项目中心取得的成绩,这是17年我们做的天瑞集团郑州水泥院公司是国家级智能试点示范。
通过刚才几个荣誉大家会看到集团的建设,每个方面都有:智能工厂、供应链各方面的业务都有,建设比较全。我们是2017年服务型制造示范企业,也是省市两级水泥工厂、物联网技术研究中心。是河南省首批行业工业互联网行业培育名单,也是刚刚通过省厅的验收。17年共有5家工厂获得智能工厂认定,18年有6家,19年有5家。
这是我们通过两化融合的工作进度,截止到19年有24家企业通过启动两化融合,已经有11家获得证书,公示阶段6家,还有7家正在审核。两化融合这一块,具体当地都有补助和支持。
回到我们今天分享的主题就是工业互联网创新。
对于流程制造特别是传统型流程制造,它的几个大的特点:我们这种行业都是重资产行业,它的设备都比较贵,所以我们总结了几条:
第一.设备得管得住,设备出一点问题都是几百万的损失。
第二.过程控制得好。生产过程不能中断,要中断成本都比较高。
第三.数据说得清,问题看得见,成本省得下,基本基于这几个主题做分享。
第一.设备管理,我们非常传统。有些去过这种工厂可能会了解,到工厂对设备的诊断是拿一个铁棒放在电机上面人去听,类似于医院的听诊器,这叫听诊棒,是听这个设备的振动。设备有没有问题,靠手摸或者去看,拿一个测温枪测温度。少量领导配测量仪,大部分靠人巡检。
客户的痛点是说大多数设备是低速重载,环境复杂,现场环境环保治理做得比较干净了,之前扬尘都是比较多的。
第二.空间限制不方便巡检。有些是高温地方,你去巡检时,人会发生事故。有些去里面检查了,过来一个高温的空气人在里面出不来了。
第三 .单台故障全线停产。它是连续生产,产量要求高,没有中间库存,中间的库存非常少。一台大的设备停机,整个生产全停。例如水泥生产中间有高温风机,它一个扇叶相当于人这么大,它出现问题之后整个都要停机,一般情况在流水线生产的企业,像这种风机一组一备,这样也不能完全保证企业连续生产。
第四.所有维修都缺乏数据,靠人去摸。有没有问题?不知道,感觉有问题,听声音不正常。这个东西很玄学,只能有专家经验的知道这个问题。
我们解决方案就是在现场装个安装大量的振动、温度、传感器,通过在系统内的制动建模,数据智能化后台的分析来去检测有没有故障?它这一块主要是对高价值的设备实时监测,准确定位故障信息。比如说里边大的减速机、轴承,一个齿轮非常大,它的中间如果产生问题你是不知道的,当然它在旋转到位置的时候会有小的冲击波,它会通过数据反馈。否则你只能把设备停掉,拆开才能知道有问题。相当于对设备做CT。 同时精确定位故障部位。
第三.减少非计划停机。以水泥企业为例,停机一天损失数百万的利润。作为水泥行业,单条生产线平均的建厂成本大概在10个亿左右,一般情况下备品备件成本在数千万、上亿。所有设备的维修,好多的备件不是标准的,你需要去定做的。你发现有故障,你再去定做,有的需要三个月到半年。
这样的话,我们通过预测维护,你去提前制定采购计划,避免停机了你没有备品备件。预判设备寿命。单次事故损失最少是50万到200万、300万之间,因为有的停下可能三个小时排除了,有的停下来三五天都排除不了,这个损失无法计算。
第二部分针对生产这一块,很多企业用户都提了,领导说第一你现在这个生产的数据我看不到,生产大多数流程行业自动化程度还是比较高的,特别是水泥行业。水泥行业所有控制的设备都是有一个DCS控制系统在中控室,当然中控室数据大部分人看不到,想看只能到中控室,中控室有门禁锁着,大家不能随便进去。这个数据,大家看不到,他们都反馈看不到。
我们通过数据采集,把所有的数据展示在每一个人员的电脑和手机端,解决数据可视化的问题还有数据分析的问题。有些人说DCS系统数据一般默认保存3到6个月,但是你要查去年的查不了,查前年的查不了,每年的工艺改造都会导致生产数据产生大量的变化,你怎么能分析你这个设备和去年的能效指标有没有更好?
对客户收益来讲,首先我们实现数据拿到了,让用户能看到了,把数据装在他的手机端口袋里边了,还可以实现一个集团的远程调度。集团企业一般对下面企业如果没有提集团管控的概念,它是不管的。你下面怎么管,自负盈亏,啥都不管。但是提集团管控的企业都要管,下面所有东西今天有没有异常,今天有没有突发性停机、不在计划的停机、事故停机。传统下面这个都隐藏了,集团都不知道,下面不报,一报就罚款。
集团也可以建调度中心,对下面所有企业数据进行实时查看。30个企业、50个企业集团配几个专家就可以把下面的企业都看到了。
同时我们把数据开放给上游-设计院。因为工艺需要每年大量改造,每年预算大概几千万的改造费用,但是怎么改造?现在的专家都飞来飞去的,飞到现场去看,就为了看你的数据,当然这个数据开放之后设计院直接可以看到。
同时还有上游的供应商,比如设备供应商,这个是谁生产的,你可以把数据提交给他,让他提前帮你分析数据,为你的项目提供服务。
数据都装在所有管理人员口袋之后,用户就开始得寸进尺了。非常简单。之前他抱怨说我看不到数据,当你把所有数据都采集之后,让他看到之后,他说我没时间看数据。
因为你数据太多了,每天都那么多数据,我天天在那看,今天是正常的,明天是正常的,我不正常的时候我没看到,晚上睡觉时有问题没看到。这时候怎么办?所以说我们现在用户的需求在得寸进尺,在变化,我们需要给他做数据分析。
员工现场办公是没有电脑的,大多数员工没有电脑,为什么说传统制造?我们很多企业的员工到现在用的还不是智能机,还有用功能机的。这个工厂在山区,它要怔地,要用当地的村民,有很多人员素质是不能做到你一招都是高中生、中专生、大学生,你能招到小学毕业都已经不错了。大部分传统制造,大部分企业可能都在山区,就需要用本地的人。你要从那过车,过运输物资你不用当地的人你是用不了的。所以说传统制造都是传统到这个程度。
我们需要把数据装在手机端还需要帮他自动分析,在这个系统里建设一个预警模型,就是工业机底模型,单纯做千篇一律还不行。不同人关注的角度、颗粒度不一样,我们现在做到千人千面,每个人在手机端自己配置。比如我是巡检共最低角色,我就关心这几个设备,那很简单,我把这一块放在我的口袋里面,有提醒我就去,没提醒我该干啥干啥。
同样对厂长他关心的是出现重大问题,对于总经理或者副总经理关心的是你现在有异常了才去管理,没有异常你让他坐这儿盯着数据那是不可能的。所以大家在数字化之后马上面临问题就是怎么智能化,如果你没有做智能化,你所有的数据都摊开之后,对业务来说是灾难。
这一块工艺的异常管控和干预我们用了一些智能化的技术,这一块减少工艺事故35%以上,做到人人都有数据,人人都有不同的标准,每年节能降耗大概1%-3%。
再到能耗这一块,所有的重工业,其实他都是一种能源的转换,特别是水泥行业,它里面主要用的电和煤。水泥的成本,电和煤的成本加在一起超过60%。我们这一块通过现场大量的能源采集、数据改造实现的采集。
最重要的是说我们把所有的数据,本来是月度数据变成日数据,日数据变成班组数据,班组数据变成小时级数据,小时级数据是指你这一小时或者这半小时能耗异常了,你都要有人查一查是什么问题,否则大家都是说有问题不去追究,到月底了这是叫正常,能耗高这叫正常。因为无法量化、考核。
讲完能耗这一块,再往上进一层次。我们的数据,能智能化分析,用户又需要分析之后要干活、操作,每个流水线都会有一个操作工岗位就是DCS控制师,他这个水平要求非常高,但是他有心情好的时候,有心情不好的时候。白天我心情好,领导在这儿我操作好一点,到晚上我累了,半个小时我都不操作。
正常生产的话,我需要把温度控制在865度上下10度范围是最优的,但是实际操作的时候我把它控制在890,控制在910、920,然后他稍微休息一会儿也没问题。温度高浪费能源,但是质量还可以,只要不是特别高。但是温度低,出来的东西就费了。
这个过程中我们自己做了一些算法,让它稳定聚焦在一个区间。因为人工操作,上边数百个参数他要看一个画面,操作得很费劲。我相信任何一个人,你再以公司为家,给你再高的收入,你在这干三年,你啥都不想弄了。特别是有些班次在现场上班,晚上到2、3点的时候,你可以看曲线。在晚上2点到4点那个曲线是最不稳的,因为晚上累,领导还都睡觉了。
所以说我们通过机底模型实现智能化控制,在后期我们还在做APC+AI优化,把AI算法加在系统里面,这一块整体来说是实现生产的稳定。所有流程制造第一要求质量稳定,第二要求生产稳定,减产就意味着成本高了。稳定生产之后可以增加产量,对每年节约能耗1%-2%,这一块是针对有些操作员的水平,你就培养不起来,他就是这样的,你让他加煤他就加,你让他减他就减,但他不问原因。大多数都是这样的情况。
这一页PPT是流程行业有大部分物资,每天生产水泥5千吨,每天进进出出原材料有上万吨,大宗的原材料进出。这种原材料进出主要靠过磅进行计量,过磅计量碰到的问题是说,原来的都是磅和ERP系统之间没有关联,中间的过程都是打印一个磅单来回传递,磅单可以造假,来的车也不一定是客户的车。当时提货单好多造的跟银票一样,要对印章、签名等,中间效率非常低。
第二.发货效率低。计重环节,车辆重复过磅,数据不准。有人的地方,一定都有江湖。
第三.偷拉错拉。在企业里面发料环节,流程行业发料环节,我开的票是35水泥,但是拉了425水泥出厂了对企业是每吨100块钱的损失。
第四.扣吨扣杂。一个收料人员一年700多万的收入不可想象,水泥行业不能这么高。大多数流程这一块收料员工资水平都不是特别高,但是是肥差,工资可能4000元到6000元,降工资都不走,但是上系统之后立马辞职,因为没有灰色收入了。把过磅所有环节做到无人值守,解决企业的跑冒低漏。
这样一做结果是企业人力成本降低15%,计量人员一个都不需要了,100%减少。一个企业有两台磅,三台磅,大概40个计量人员。业务岗位人员工作强度降低70%,纸制票据降低5%,业务管控提升50%。老板最喜欢问上系统之后有什么价值,其实价值很难分析,很多价值很难量化。你说这个企业每年被偷拉走多少货?哪个老板承认,哪个管理人员承认?跑冒低漏的东西一定会通过盘损来把账做平,你看不到损失,但是老板可以看到损失,所以跟老板沟通他的需求很明确。
云计量,我们主要是通过SaaS部署,把产品改变一下,合作模式改为按车次计费,用户不用做前期硬件投入,这一块投入可以由我们自己来做。
我们天瑞做的项目和系统和华为一样,自己造的降落伞自己先跳,自己用得好再向其他的行业客户进行推广。
这一部分是网络货运,刚才讲的那一块都是厂内的物流,但是厂内物流出厂之后是不是都失去管控了?你的上游采购环节,下游销售环节是否需要管控?当然这一块管控的内容比较多,我们只是抓了其中几大重要部分。
针对这个货主企业它的信息不透明、层层转包,你的货不知道转包多少层了,转包一次一个车被收100元不等。
对物流公司来说找货难,天天有车找不到货,这个货比如运到山西回来是空车,结算难、开票难。很多传统流程制造都是月结、季结、年结,账是压着的,前期不结算相关费用。
信息不透明,车辆利用率高。大多数司机买车挂靠一个公司,好多人员操作水平或者是信息化水平都不是特别高。
虚开漏开发票,好多运输行业,我跑运输没有发票,这个发票都是去找运输公司源的票。本来是完全真实的业务最后变成了不合法的业务。对于税务系统来说,只要查到这都是违反税法的。
政府部门数据监控、整合困难,业务发生地、税收分离。本来你的运输地发生在河南,但是运输公司在内蒙,发票开到内蒙去了,等于水源外流。
我们核心问题还是开具核心的合规的运输发票,包括整个平台对物流业务的运输管理。
这一块的价值就是车辆利用率提高85%,车辆空驶率降低20%,车货匹配从2天降低到8小时,运输成本15%-20%,安全事故小于千分之一。因为我们在乘运货默认赠一个货物险。累计交易额100多亿。
矿山这一块对5G要求比较多的特殊的场景,矿山的处量都是人工统计,无序开采矿山资源进行浪费。原来有一个是废石,现在利用这个废石粉碎之后叫鼓料或者叫粉碎成沙。还有的位置偏僻、爆破多,最重要的工程机械多,安全隐患大。矿山行业只要出一次安全事故,直接停产,甚至是没有协商的可能性。大家搞流程制造,特别像我们这个行业,如果没有矿山,这个企业就不用开。
我们通过建设安全底座、无人驾驶,三维的数字化开采系统包括智能调度相关系统实现整个矿山一体化的数字化管控。主要是稳质提效增产降本安全。
对客户的收益主要是提高矿山生产效率,降低油耗、优化人员、提升资源利用率,最重要的是管控安全,第二才是管控我的资源的利用率。
对于天瑞来说,它是非常传统的制造,但是通过刚才的分享是希望给各位CIO传达一个概念,其实传统企业也可以走向科技型企业。所以我们对很多的企业理念还认为首先企业从内部打通,把内部所有的系统实现一个互联互通,内部通了之后需要走上下游,把上游、下游进行打通,联通起来、互联,最后搭建一个平台。
关于中台的概念,其实前边各位大咖都已经讲了很多了,不管是中台还是后台还是前台,其实未来的系统都是互联网化的思维。我们有互联网的基因,不能完全去纠结于我要不要建一个中台,为什么呢?因为我们最终客户、用户的需求是我们的衣食父母,我们CIO存在的价值就是满足用户的需求。所有的技术都不是核心,最终的核心是让用户满意。
我的分享完毕,谢谢!